Many manufacturers continuously look for ways to streamline manufacturing operations. After all, time saved means money saved when running a business. Managing the operations of a manufacturing company isn’t the same as managing a typical office-based company.
The daily operations in a manufacturing plant can be highly complex, with several mechanical components. Often, this complexity can lead to shortfalls and impediments down the road. In general, it may be to blame for slowing down your business and putting you behind the competition. With this in mind, it’s critical to understand the best methods for streamlining manufacturing operations.
Streamlining To Improve Operations.
Remember that there are several areas you should concentrate on to ensure that they have a significant impact on your business and workforce while also increasing your chances of reaching new heights in the long run. Manufacturers who want to streamline highly complex operations see it as a critical goal to save money and time while increasing overall productivity and profitability. Unfortunately, streamlining long-established processes can be a time-consuming and daunting task.
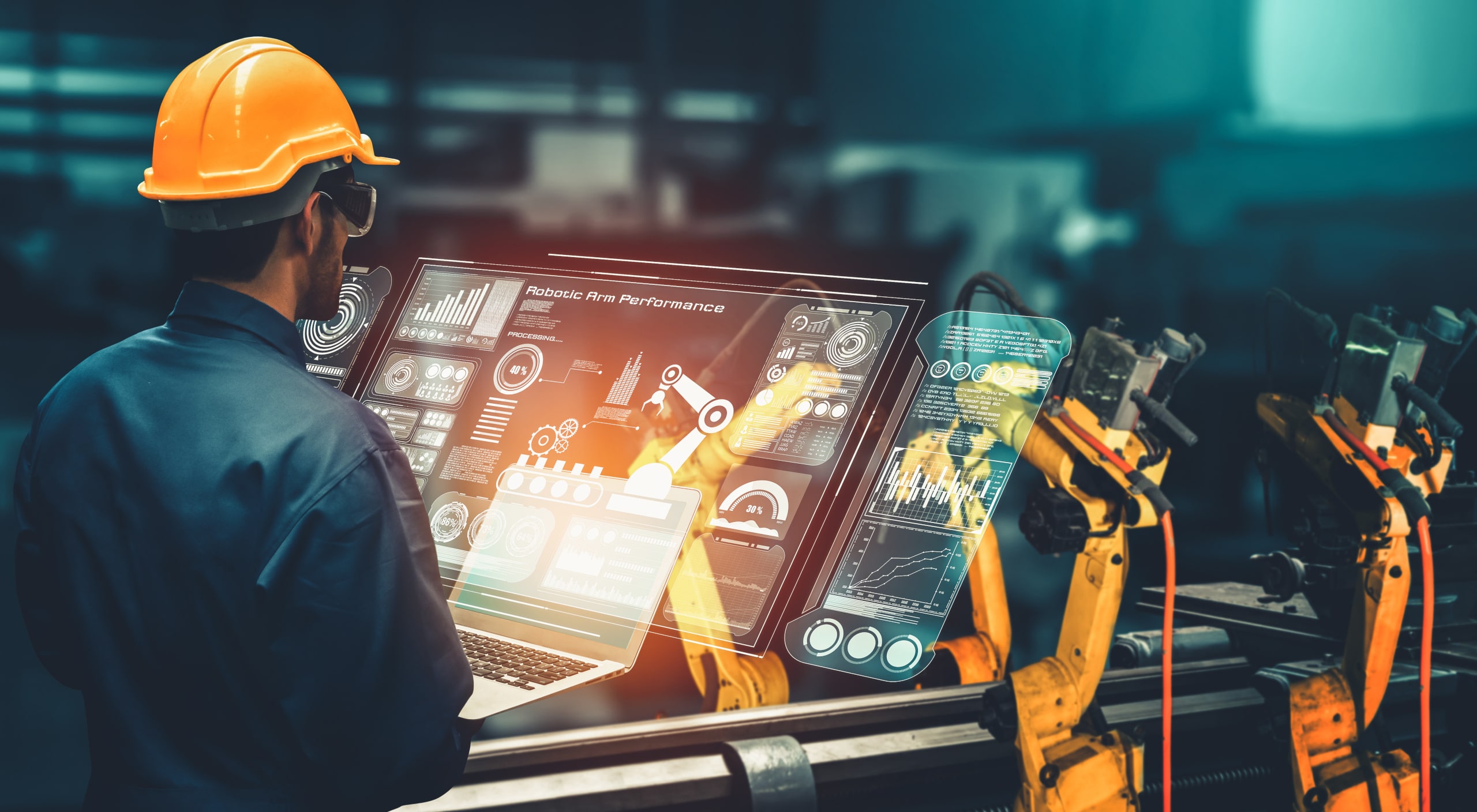
Make an effort to invest in proper quality programs and new technologies right from the start. It may make it easier to improve current processes and see immediate results. An example is production scheduling software for manufacturing, making the production planning manageable and streamlining your business’s manufacturing operations.
There are various ways to streamline the manufacturing processes to pave the path for seamless operations and workforce efficiency. Here are a few crucial points to get you started on the right track toward streamlining your company’s manufacturing operations:
1. Conduct a Thorough Assessment of the Manufacturing Operations.
Once you’ve decided to streamline your manufacturing operations, the best place to start is by determining the overall state of your operations. Make an effort to assess project timelines, material orders, fulfilled and missed deadlines, accounting, partner agreements, and all systems in place to identify strengths, weaknesses, and opportunities for improvement.
Reviewing these items based on real figures and results will help you make the right decisions. If your current data-tracking methods are no longer effective, consider switching to a manageable platform capable of seamless measuring, comparing, and analyzing the results.
The method enables you to examine tangible, factual proof of logical areas for cost reduction. With the data you have, you can also focus on process optimization, workflow simplification, or investment in new equipment, software, or suppliers.
2. Invest in Better Machinery.
Investing in better machines—if your budget allows it—is one of the first steps to consider if you want to streamline your manufacturing operations. Generally, your equipment plays a crucial role in keeping your company operational. Shifting to more reliable and accurate models will improve the general processes and the finished products greatly regardless of the type of product you specialize in.
3. Better Quality Control.
Quality control is a critical element in the manufacturing industry. When several products fail to comply with the requirements, they waste both time and resources. One way to improve quality control is to maintain a clean and tidy workspace, test equipment regularly, and assemble a talented crew with ongoing training in quality control.
4. Find Ways To Minimize Waste.
Excessive waste production is something to avoid if you want to maintain an efficient workspace. The waste takes up precious space and causes a drop in profits over time. An effective way to avoid this is to prioritize inventory management and cut down on resources.
Aside from the resources that go to waste, it also consumes your workforce’s time. If you want to ensure the productivity of your employees, consider investing in time management tools.
It’s critical to fully comprehend what is truly important to overall performance and ensure alignment with business decisions. Inventory, data redundancy, overproduction, system downtime, correction of errors, and other factors can all contribute to waste.
5. Make the Most out of Manufacturing History Data.
Manufacturers should maximize technology to meticulously assess various factors, such as the number of resources used, the amount ending up as scrap or waste, and the time spent on the overall manufacturing process. You’ll need to carefully review the current purchase orders of materials and dispatching steps to ensure accuracy. Following that, it’s critical to keep track of resource usage and overall production time.
Make the task of scrutinizing the manufacturing history data a priority for this process, involving all crucial teams. It can help you fully understand how to make modifications to save time and resources throughout manufacturing phases by thoroughly analyzing past performance.
6. Implement the Right Quality Program or Software.
One way to help streamline manufacturing operations is to utilize the right quality software or program. Having a reliable one will help ensure that the correct products are available when required, maximizing overall productivity.
The cost of materials, the routing steps, and the time it’ll take to complete them should all be confirmed in the quality program. Furthermore, it should aid in waste reduction by presenting knowledge on the materials to use to lessen scrap.
7. Improve Team Communications.
The quality of communication in a manufacturing company is a crucial factor to consider. Poor communication can disrupt the manufacturing process. Luckily, several ways can help improve communications, including the integration of technology.
Today, you might want to invest in the latest technological trends such as communication software, radios, and wearables to ensure a more streamlined workforce capable of reaching different team channels. When each team can connect with another seamlessly, your team can get more things done in a day.
8. Workplace Decluttering.
It can be difficult to accomplish critical tasks in an unkempt environment, particularly on the production floor. Due to this, you need to maintain a clutter-free workspace.
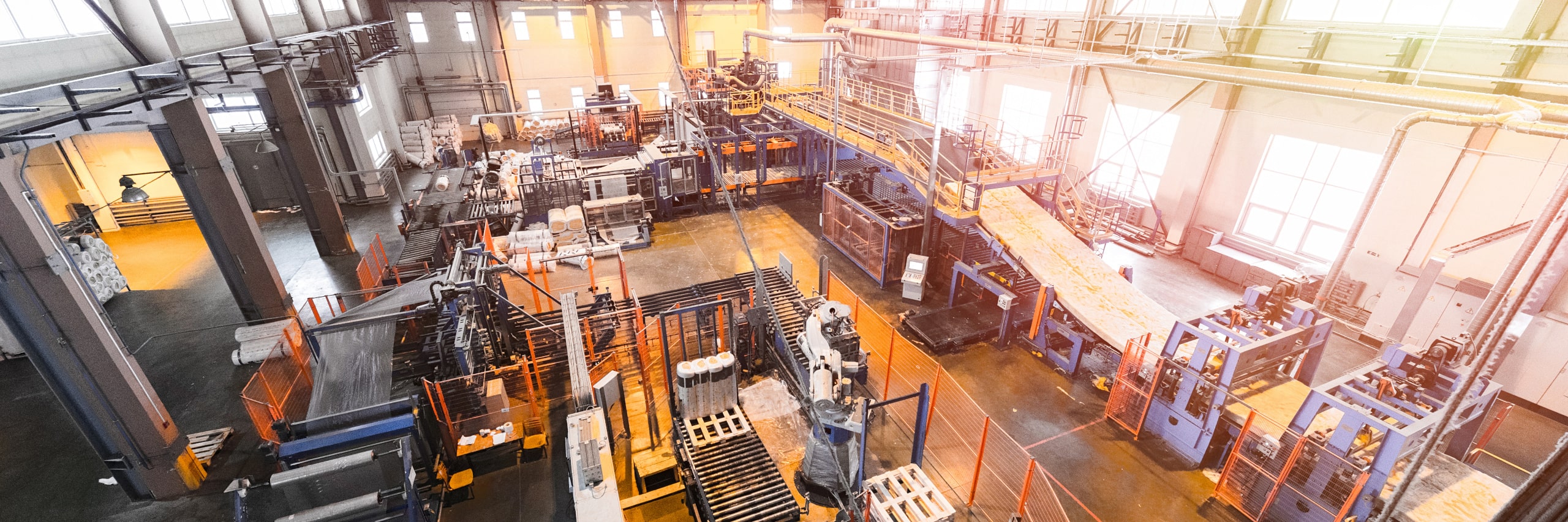
One way to make this happen is to schedule a monthly decluttering routine of the entire work area to ensure tidiness. It’s best to include this in the routine maintenance checks to ensure the efficiency and productivity of both the machinery and your workforce.
9. Repair Any Broken Equipment or Machinery.
Manufacturing operations are at high risk of stalling if equipment begins to deteriorate or malfunction. If you have several critical pieces of equipment in the manufacturing process, they’re more likely to fail at an inconvenient time or when you least expect them.
Critical equipment failure can put your operations on hold until repairs are made promptly. If repeated problems arise, it will result in frequent downtime for your manufacturing operations.
The best solution is to determine which equipment is critical to daily operations and invest in exact models to ensure minimal downtime. When current machinery begins to underperform or fails to operate normally, another can take its place while one of your teams is still fixing its problems. Most manufacturing companies take this approach to ensure as little downtime as possible.
10. Deadlines Should Be Strictly Adhered To.
A common bottleneck that disrupts manufacturing operations is a lack of understanding of deadlines, roles, and responsibilities within a company. Make it a priority to implement clear and attainable deadlines to help streamline the crucial processes.
You need to set reasonable and attainable deadlines. Remember that not every step or phase should be under a tight deadline since this unnecessarily constricts workflows and becomes stressful for your workforce.
11. Prioritize the Health of Your Workforce.
While it’s crucial to provide proper care and maintenance of your equipment, ensuring your employees are in good health and well-being is equally important. The global pandemic had a negative impact on many manufacturing companies around the world. A single employee becoming ill can bring the entire operation to a halt.
Set a high bar for employee health and take the necessary precautions to keep everyone in your facility safe. Providing your workforce with personal protective equipment (PPE) is the best way to prevent the spread of any illnesses.
Another way to protect your employees is to recognize the tell-tale symptoms before they spread. By scanning staff and visitors for elevated body temperatures with non-invasive measures such as temperature stations deployed at entry points, you can streamline operations and promote employee health and safety.
12. Initiate a Pilot Program.
Focusing on any underperforming product line is one way to streamline manufacturing operations. Underperforming products should be chosen as test subjects for further investigation because they are more likely to suffer from poor quality, production issues, fulfillment problems, and other issues.
Once you pinpoint such product lines, you can learn crucial insights representing more comprehensive process modifications. After gathering insights from pilot data, you can utilize the information to create a plan of action to make the necessary modifications or improvements.
13. Make the Transition to Paperless Operations.
Another way to streamline manufacturing operations is to go paperless. Having large amounts of paper in the workspace is a waste of time and can be detrimental to the environment. Once you decide to shift to paperless operations, you can store all files digitally. Doing so cuts down on the effort of going through piles of paperwork and provides one library from which all your staff can find all the documentation they need.
Final Thoughts.
In the manufacturing industry, streamlining operations must be one of the top priorities to ensure your business stands out from the competition and maintains a high level of efficiency. Taking these tips into consideration when streamlining your business’s operations will ensure the seamless flow of processes for better efficiency and profits in the long run.
Leave a Reply