In industries where machinery forms the heartbeat of operations, downtime is more than a minor inconvenience—it can be a major blow to productivity and profits.
So, how do businesses keep their mechanical partners in top shape?
The answer lies in adopting forward-thinking maintenance strategies that not only fix issues but predict and prevent them. Here are six savvy techniques that can keep your machines humming smoothly, reducing stress on both the equipment and your bottom line.
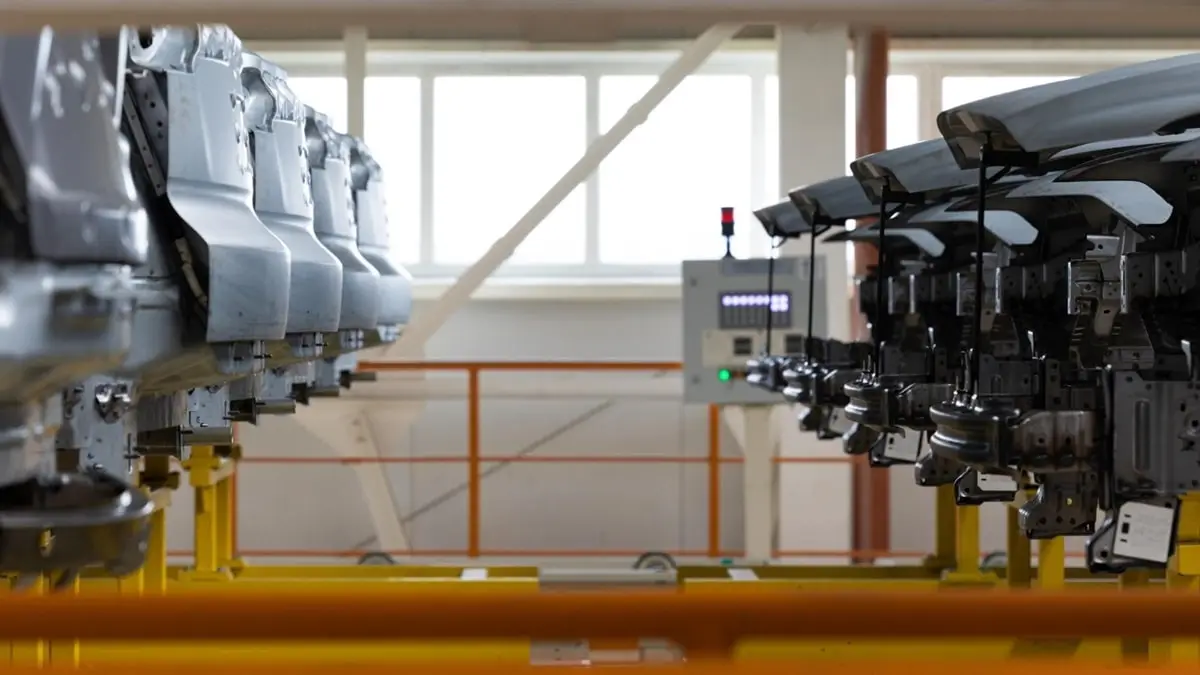
1. Regular Preventive Maintenance.
Regular Preventive Maintenance (PM) is a proactive strategy that is essential to optimizing equipment uptime. Through regular scheduling of inspections and servicing, companies can guarantee that all parts are operating at peak efficiency and that possible issues are addressed before they become expensive breakdowns.
In addition to standard maintenance like cleaning and lubrication, this procedure entails thorough inspections and the replacement of components that are prone to wear and strain.
Frequent preventive maintenance extends the operational life and efficiency of machinery by recognizing the operational demands of each piece of equipment and customizing the maintenance actions to meet these needs.
It goes beyond simply mending things before they break.
2. Upgrade to Smart Sensors.
Integrating smart sensors into industrial equipment ushers in an era of enhanced monitoring and predictive analytics, which are cornerstone elements of modern maintenance strategies.
These sophisticated devices actively collect real-time data on essential operational parameters, including temperature, pressure, load cycles, and even humidity levels.
This wealth of information feeds into advanced predictive models that assess the condition of machinery, forecasting potential breakdowns with remarkable accuracy.
When these sensors are connected to IoT platforms, they enable a seamless flow of data that triggers automated alerts and actions, greatly enhancing the precision and timeliness of maintenance efforts. Due to this automation, we save a lot of resources and time.
Furthermore, by enabling remote monitoring, maintenance supervisors can observe the condition of the equipment from any location, which eliminates the need for on-site inspections. By switching to smart sensors, you may substantially reduce unplanned downtime and reduce the frequency of manual inspections. This will streamline your maintenance procedures and guarantee more constant operational efficiency.
3. Implement Comprehensive Diagnostic Analyses.
Adopting a broad spectrum of diagnostic analyses is key to understanding and improving the health of machinery. This approach encompasses a variety of techniques, each tailored to detect specific types of potential issues before they escalate into major failures.
Techniques can include, for instance—thermal imaging to spot heat anomalies, oil analysis to check for contaminants or wear particles, and ultrasonic testing to identify leaks or flaws in high-pressure systems. Among these analyses techniques, effective vibration analysis is particularly effective for rotating equipment, providing critical insights into component condition and helping prevent failures. Utilizing these diagnostic tools allows maintenance teams to take a more informed, targeted approach to machine upkeep, ensuring optimal performance and extended equipment lifespans.
4. Staff Training and Empowerment.
Keeping high equipment uptime requires empowering the workers with thorough training programs. A crew with a high level of education can identify the early indicators of equipment failure, comprehend the workings of complicated machinery, and efficiently complete necessary maintenance duties. By funding continual training, employers may make sure that employees are knowledgeable on the newest tools and upkeep methods.
Team members are motivated to take the initiative to maintain the health of the equipment as a result of this empowerment, which creates a proactive and safe workplace culture.
Frequent training sessions also improve team cohesiveness and productivity, which are critical components for prompt and efficient problem-solving in the event that machinery malfunctions. Business leaders are often key players here, as they are top motivators.
In addition to providing employees with the skills they need, enhanced training fosters a sense of accountability and ownership for the equipment they use. This heightened engagement leads to more diligent care and maintenance practices, significantly boosting overall equipment effectiveness and reliability.
5. Streamline Maintenance Procedures.
Reducing equipment downtime requires optimizing maintenance protocols. Businesses can streamline these procedures and concentrate on critical maintenance tasks that have a direct influence on equipment performance by getting rid of pointless stages. Using management software can be quite helpful in this situation since it keeps track of repair history, organizes maintenance schedules, and guarantees that work is done to a high standard and on time.
Simplified processes help to maintain a uniform standard throughout all operations, while also increasing the efficiency and speed of maintenance efforts.
Maintaining consistency is essential for preventing mistakes and making sure that each piece of equipment gets the care it needs to function reliably.
6. Optimize Maintenance Scheduling with AI.
Leveraging artificial intelligence (AI) to optimize maintenance scheduling represents a groundbreaking advancement in equipment management.
AI algorithms can analyze vast amounts of data from machine operations, maintenance histories, and sensor outputs to identify patterns and predict optimal maintenance times.
This technology enables companies to transition from routine or calendar-based maintenance to a more efficient, condition-based strategy. By scheduling maintenance only when the data indicates it is necessary, businesses can avoid unnecessary downtime and focus resources more effectively. AI-driven scheduling also adapts to changes in equipment usage and environmental conditions, ensuring that maintenance aligns with actual wear and tear rather than arbitrary timelines. This approach not only extends the life of the equipment but also maximizes operational availability, keeping productivity levels high.
Embracing these six techniques doesn’t just improve equipment uptime; it transforms how teams approach maintenance, turning reactive practices into proactive strategies. This shift is essential in a world where every minute of production counts and the cost of downtime soars. More importantly, these methods build a foundation for a resilient operational future, where equipment reliability is a given, not a gamble. It’s about making smart, strategic decisions that keep the wheels turning and ensure they do so more smoothly than ever.
Leave a Reply